Inventory Management Systems in Business Accounting
+business +inventory +accounting +application – Effective inventory management is crucial for the financial health of any business. Accurate tracking of inventory levels directly impacts profitability, operational efficiency, and the accuracy of financial reporting. This section explores different inventory accounting systems and their implications.
Inventory Accounting System Types: Periodic vs. Perpetual
Businesses employ two primary inventory accounting systems: periodic and perpetual. Each has distinct features, advantages, and disadvantages.
Feature | Periodic System | Perpetual System |
---|---|---|
Inventory Count | Physical count conducted periodically (e.g., monthly, quarterly) | Continuous tracking of inventory levels through real-time updates |
Cost of Goods Sold (COGS) Calculation | Calculated at the end of the period based on the beginning inventory, purchases, and ending inventory | Calculated with each sale, providing immediate COGS information |
Accuracy | Lower accuracy due to reliance on periodic physical counts | Higher accuracy due to continuous monitoring |
Cost | Generally less expensive to implement | Requires more sophisticated software and potentially more labor |
Complexity | Simpler to implement and manage | More complex to set up and maintain |
Impact of Inaccurate Inventory Data on Financial Reporting
Inaccurate inventory data can significantly distort a company’s financial statements. Overstated inventory leads to inflated assets and understated cost of goods sold, resulting in higher reported profits. Conversely, understated inventory leads to understated assets and overstated cost of goods sold, resulting in lower reported profits. This inaccuracy can mislead investors, creditors, and management, hindering informed decision-making.
Implementing a New Inventory Management System
Implementing a new inventory management system requires careful planning and execution. This process typically involves needs assessment, software selection, data migration, user training, and ongoing system maintenance. Integration with existing accounting software is a key consideration.
- Needs Assessment: Identify current inventory management challenges and desired improvements.
- Software Selection: Choose a system that aligns with business needs and budget.
- Data Migration: Transfer existing inventory data into the new system accurately.
- User Training: Provide comprehensive training to staff on using the new system.
- System Testing: Thoroughly test the system before full implementation.
- Go-Live and Ongoing Maintenance: Launch the system and provide ongoing support and maintenance.
Integrating Inventory Accounting Applications with Existing Business Software
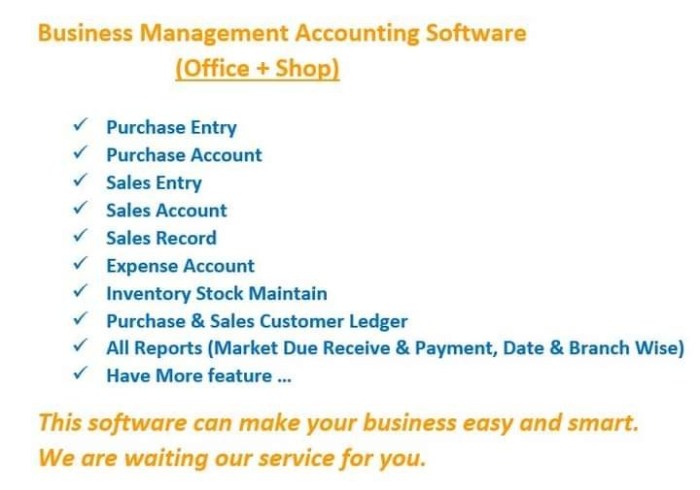
Source: ptshopbd.com
Seamless integration between inventory accounting applications and existing business software is essential for efficient data flow and accurate financial reporting. This section explores different integration methods and associated security considerations.
Integration Methods: APIs vs. Manual Data Entry
Two primary methods exist for integrating inventory accounting applications: Application Programming Interfaces (APIs) and manual data entry. APIs offer automated, real-time data exchange, while manual data entry is prone to errors and requires significant manual effort.
- APIs: Automated data exchange, reducing errors and improving efficiency. Requires technical expertise for setup.
- Manual Data Entry: Time-consuming, error-prone, and inefficient. Suitable only for small businesses with minimal transactions.
Security Considerations in System Integration
Integrating inventory and accounting systems necessitates robust security measures to protect sensitive financial data. This includes secure data transmission protocols, access control measures, and regular security audits. Encryption of data both in transit and at rest is paramount.
API Integration Configuration: A Step-by-Step Guide
Configuring an API integration involves several steps, including obtaining API credentials, understanding the API documentation, and testing the integration. Specific steps will vary depending on the software used. A general Artikel is provided below.
- Obtain API keys and authentication credentials from both the inventory and accounting software providers.
- Review the API documentation for both systems to understand the available endpoints and data formats.
- Develop or use pre-built integration tools to establish a connection between the systems.
- Test the integration thoroughly by exchanging sample data and verifying its accuracy.
- Implement error handling and logging mechanisms to monitor the integration’s performance.
- Document the integration process for future reference and troubleshooting.
Cost Accounting and Inventory Valuation Methods
Accurate inventory valuation is crucial for determining the cost of goods sold (COGS) and ultimately, a company’s profitability. Several methods exist, each with its own implications for financial reporting.
Inventory Valuation Methods: FIFO, LIFO, Weighted-Average Cost
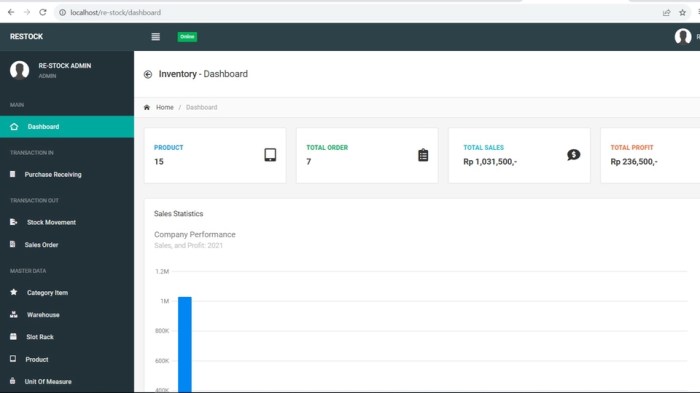
Source: fastwork.co
Three common inventory valuation methods are First-In, First-Out (FIFO), Last-In, First-Out (LIFO), and Weighted-Average Cost. The choice of method impacts the reported COGS and net income.
- FIFO (First-In, First-Out): Assumes that the oldest inventory items are sold first. Example: If 10 units were purchased at $10 each and 5 more at $12 each, the COGS for 8 units sold would be (8*$10) = $80 under FIFO.
- LIFO (Last-In, First-Out): Assumes that the newest inventory items are sold first. Example: Using the same example, the COGS for 8 units sold would be (5*$12)+(3*$10) = $90 under LIFO.
- Weighted-Average Cost: Calculates the average cost of all inventory items and uses this average to determine COGS. Example: The average cost is (($10*10)+($12*5))/15 = $10.67. The COGS for 8 units would be (8*$10.67) = $85.36.
Impact of Inventory Valuation Method on Financial Statements
The choice of inventory valuation method directly affects the reported cost of goods sold (COGS) and net income. FIFO generally results in higher net income during periods of inflation, while LIFO results in lower net income. Weighted-average cost provides a middle ground.
Cost of Goods Sold (COGS) Calculation
COGS is calculated differently depending on the inventory valuation method chosen. The formulas are:
- FIFO: COGS = Cost of oldest inventory sold
- LIFO: COGS = Cost of newest inventory sold
- Weighted-Average Cost: COGS = (Number of units sold)
– (Weighted-average cost per unit)
Inventory Control and Forecasting Techniques
Effective inventory control and forecasting are vital for optimizing inventory levels, minimizing costs, and meeting customer demand. This section explores key performance indicators (KPIs) and forecasting techniques.
Key Performance Indicators (KPIs) for Inventory Management
Several KPIs are used to monitor inventory levels and efficiency. These metrics provide insights into inventory turnover, stockouts, and obsolescence.
KPI | Description | Formula | Ideal Range |
---|---|---|---|
Inventory Turnover | Measures how efficiently inventory is sold | Cost of Goods Sold / Average Inventory | Varies by industry, generally higher is better |
Days Sales of Inventory (DSI) | Number of days it takes to sell inventory | Average Inventory / (Cost of Goods Sold / 365) | Varies by industry, lower is generally better |
Stockout Rate | Percentage of times an item is out of stock | Number of stockouts / Total number of demand requests | As close to 0% as possible |
Inventory Holding Cost | Cost of storing and maintaining inventory | (Storage costs + Insurance + Taxes + Obsolescence) / Average Inventory Value | Lower is better |
Simple Inventory Forecasting Model
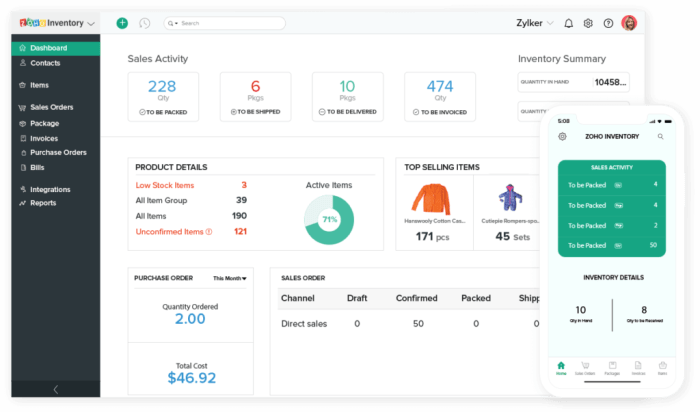
Source: selecthub.com
A simple inventory forecasting model can be built using historical sales data and trend analysis. This involves analyzing past sales patterns to predict future demand. More sophisticated models may incorporate seasonality, economic factors, and other variables.
Example: A simple moving average can be calculated using the average sales of the past three months to forecast the next month’s sales. If sales were 100, 110, and 120 units in the past three months, a simple forecast for the next month would be (100+110+120)/3 = 110 units.
Preventing Inventory Shrinkage and Obsolescence
Inventory shrinkage (loss due to theft, damage, or error) and obsolescence (loss due to outdated or unsaleable items) can significantly impact profitability. Implementing robust inventory control measures, regular stocktaking, and effective demand forecasting can mitigate these risks.
The Role of Technology in Modern Inventory Accounting
Technology plays a crucial role in modern inventory accounting, improving accuracy, efficiency, and decision-making. This section explores the use of barcode scanning, RFID technology, and cloud-based applications.
Barcode Scanning and RFID Technology in Inventory Management
Barcode scanning and Radio-Frequency Identification (RFID) technology automate inventory tracking, eliminating manual data entry and improving accuracy. Barcode scanners read barcodes on products, while RFID tags transmit data wirelessly, allowing for real-time tracking of inventory movement.
Barcode scanning provides a relatively inexpensive and simple method for tracking inventory. RFID offers more advanced capabilities, including tracking multiple items simultaneously and providing more detailed information about each item’s location and status. RFID is particularly beneficial in environments with high inventory volume or fast-moving goods.
Cloud-Based Inventory Accounting Applications: Benefits and Drawbacks
Cloud-based inventory accounting applications offer several benefits, including accessibility, scalability, and reduced IT infrastructure costs. However, they also present drawbacks, such as reliance on internet connectivity and potential security concerns.
- Benefits: Accessibility from anywhere, scalability to accommodate growth, reduced IT infrastructure costs, automatic updates.
- Drawbacks: Reliance on internet connectivity, potential security vulnerabilities, vendor lock-in, potential monthly subscription costs.
Workflow of a Modern Inventory Management System
A modern inventory management system streamlines the entire process from purchase order to sales invoice. The workflow typically involves purchase order creation, goods receipt, inventory storage, order fulfillment, shipping, and invoicing. Each stage is digitally tracked, providing real-time visibility into inventory levels and movement. Data is automatically updated across the system, ensuring accuracy and efficiency. The system integrates with other business software, such as accounting and CRM systems, providing a holistic view of the business.
Auditing Inventory and Accounting Records: +business +inventory +accounting +application
Regular inventory audits are essential for verifying the accuracy and reliability of inventory records and preventing fraud. This section Artikels audit procedures and common discrepancies.
Inventory Audit Procedures, +business +inventory +accounting +application
Conducting an inventory audit typically involves a physical count of inventory, comparison of physical counts to recorded inventory levels, investigation of discrepancies, and documentation of findings. The audit should be performed by independent personnel to ensure objectivity.
- Planning: Define the scope and objectives of the audit.
- Physical Count: Conduct a thorough physical count of inventory items.
- Reconciliation: Compare physical counts to recorded inventory levels.
- Investigation: Investigate any discrepancies found.
- Documentation: Document all findings and conclusions.
Common Errors and Discrepancies in Inventory Audits
Common errors and discrepancies found during inventory audits include inaccurate record-keeping, theft or loss, damage to inventory, and obsolescence. These discrepancies can lead to misstatements in financial statements and hinder accurate decision-making.
Best Practices for Maintaining Accurate Inventory Accounting Records
Maintaining accurate inventory accounting records requires a combination of robust systems, procedures, and employee training. This includes implementing an inventory management system, conducting regular physical counts, reconciling inventory records, and providing employee training on proper inventory handling procedures.
Quick FAQs
What are the potential consequences of using outdated inventory accounting software?
Outdated software can lead to inaccurate data, compliance issues, inefficient processes, and increased risk of errors, ultimately impacting financial reporting and decision-making.
How often should inventory audits be conducted?
The frequency of inventory audits depends on factors like business size, industry, and inventory turnover rate. However, annual audits are a common practice, with more frequent checks potentially needed for high-value or high-risk items.
What is the best way to handle inventory shrinkage?
Strategies to mitigate shrinkage include robust security measures, regular cycle counts, employee training, and implementing strong internal controls.
Can I use a spreadsheet for inventory management in a small business?
Spreadsheets can work for very small businesses, but they become inefficient and prone to errors as the business grows. Dedicated inventory management software offers scalability and better features.