Annual Inventory Count: A Business Definition: Annual Inventory Count Business Definition
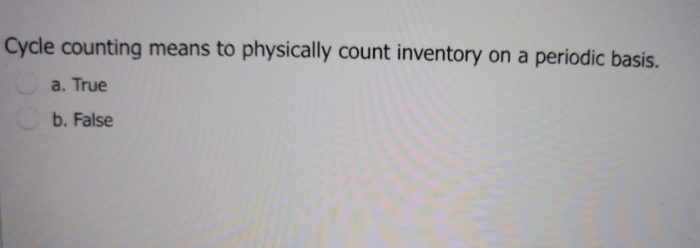
Source: cheggcdn.com
Annual inventory count business definition – An annual inventory count is a crucial process for businesses of all sizes, involving the physical verification and quantification of all goods and materials held in stock at a specific point in time. This process plays a vital role in ensuring the accuracy of financial reporting, informing strategic business decisions, and maintaining operational efficiency. Accurate inventory data provides a clear picture of a company’s assets and liabilities, influencing everything from production planning to sales forecasting.
Definition and Purpose of Annual Inventory Count
The core business definition of an annual inventory count is the systematic process of physically counting and verifying all items in a company’s inventory at the end of a fiscal year. This contrasts with perpetual inventory systems which maintain continuous records. The purpose is to reconcile the physical inventory with the recorded inventory levels, identifying any discrepancies and ensuring the accuracy of financial statements.
Accurate inventory counts are paramount for financial reporting. Incorrect counts directly impact the balance sheet (inventory valuation) and the income statement (cost of goods sold). Overstated inventory inflates assets and understates expenses, while understated inventory has the opposite effect, potentially leading to inaccurate profit calculations and tax liabilities.
Businesses requiring annual inventory counts include retailers (clothing stores, supermarkets), manufacturers (auto parts, electronics), wholesalers (food distributors, building supplies), and even service-based businesses that hold significant inventory of parts or supplies. The frequency and intensity of counts depend on the nature and value of the inventory.
Consequences of inaccurate inventory counts can be severe. These include financial misreporting leading to legal issues, inaccurate cost of goods sold calculations impacting profitability assessments, poor inventory management leading to stockouts or overstocking, and inefficient resource allocation due to flawed data.
Perpetual vs. Periodic Inventory Systems
Feature | Perpetual Inventory System | Periodic Inventory System | Annual Count Relevance |
---|---|---|---|
Inventory Tracking | Continuous tracking of inventory levels | Inventory levels tracked periodically | Less frequent, used primarily for reconciliation. |
Counting Frequency | Frequent updates; may involve cycle counting | Inventory counted at specific intervals (e.g., annually) | Crucial for year-end financial reporting. |
Accuracy | Generally higher accuracy due to continuous tracking | Accuracy depends on the frequency and thoroughness of the physical count | Helps verify the accuracy of periodic records. |
Cost | Higher initial investment in technology and systems | Lower initial investment, but potentially higher costs due to larger physical counts | Cost-benefit analysis crucial in deciding frequency. |
Methods and Procedures for Conducting an Annual Inventory Count
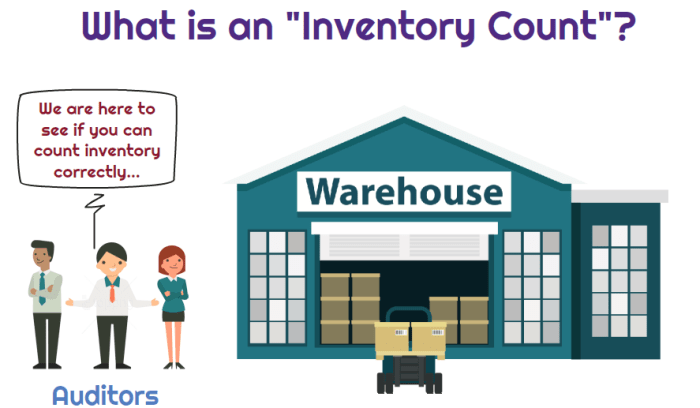
Source: universalcpareview.com
Several methods exist for conducting an annual inventory count. Cycle counting involves counting a small portion of the inventory regularly, reducing the burden of a large, single count. A full physical count, however, involves counting all inventory items simultaneously, offering a complete snapshot.
A full physical inventory count involves detailed planning and execution. This includes assigning teams, defining counting procedures, establishing clear communication channels, and developing a detailed checklist. The process typically begins with preparation – organizing the warehouse, gathering necessary equipment, and training staff. The actual count follows a structured approach, with team leaders verifying counts and resolving discrepancies. Post-count reconciliation and analysis complete the process.
Step-by-Step Procedure for a Typical Annual Inventory Count, Annual inventory count business definition
- Planning and Preparation: Define scope, assign teams, create checklists, gather supplies.
- Training: Train all staff on counting procedures, using scanners, and resolving discrepancies.
- Pre-Count Activities: Organize the warehouse, label shelves, and ensure all items are accessible.
- Counting: Teams count inventory items, using scanners to record data.
- Verification: Team leaders verify counts and resolve discrepancies on-site.
- Data Entry: Data from scanners is uploaded and reconciled with existing inventory records.
- Reconciliation and Analysis: Identify and investigate discrepancies.
- Reporting: Generate reports summarizing findings and variances.
Essential Materials and Equipment
- Barcode scanners or RFID readers
- Counting tags or labels
- Clipboards and pens
- Inventory count sheets
- Calculators
- Mobile devices (tablets or smartphones)
- Inventory management software
Barcode scanners and RFID technology significantly improve efficiency. Barcode scanners quickly record item information, minimizing manual data entry errors. RFID tags allow for faster, more accurate counting of larger quantities, particularly for items that are difficult to individually scan.
An annual inventory count, a crucial business process, provides a snapshot of a company’s assets. Understanding the results often involves analyzing trends, such as an increase in business inventories , which might indicate strong sales projections or potential overstocking. This data, gathered during the annual count, is then used for financial reporting and informed decision-making regarding future purchasing and production.
Challenges and Best Practices in Inventory Counting
Common challenges during annual inventory counts include time constraints, staffing limitations, and ensuring data accuracy. These challenges can lead to errors, discrepancies, and ultimately, inaccurate financial reporting. Effective strategies are crucial to mitigate these issues.
Minimizing errors and discrepancies involves thorough planning, clear procedures, trained staff, and the use of technology. Implementing robust quality control measures throughout the counting process helps maintain data integrity. Regular cycle counting reduces the burden of a large annual count and identifies discrepancies early on.
Best practices include using standardized procedures, cross-checking counts, implementing a robust error-correction process, and utilizing inventory management software to streamline the process and improve accuracy. Software solutions vary in functionality and cost; selecting a system that meets specific business needs is crucial.
Proper staff training is paramount. Staff should be well-versed in counting procedures, using scanning equipment, and resolving discrepancies. Regular training and refresher courses ensure consistent accuracy and efficiency.
Inventory Management Software Solutions
Various inventory management software solutions exist, ranging from simple spreadsheet programs to sophisticated enterprise resource planning (ERP) systems. These systems offer features like barcode scanning integration, real-time inventory tracking, and automated reporting. The choice of software depends on the size and complexity of the business and its inventory.
Post-Count Reconciliation and Analysis
Reconciling the physical inventory count with existing inventory records is a critical step. This involves comparing the physical count data with the recorded inventory levels in the system, identifying any variances.
Common discrepancies include counting errors, data entry errors, theft, damage, or obsolescence. Investigating these discrepancies requires careful analysis, potentially involving reviewing security footage, examining transaction records, and physically inspecting the affected items.
Methods for resolving discrepancies involve re-counting, verifying data entry, investigating potential causes (theft, damage, etc.), and adjusting inventory records accordingly. A well-defined process for investigating and resolving discrepancies is crucial for maintaining data accuracy.
Reconciliation Flowchart
(Note: A visual flowchart would be included here in a real-world application. Due to the limitations of this text-based format, a textual description is provided instead.) The flowchart would begin with the completion of the physical inventory count. The next step would be the comparison of the physical count data with the existing inventory records. Any discrepancies would trigger an investigation process involving re-counting, reviewing security footage, and examining transaction records.
The resolution of discrepancies would lead to the adjustment of inventory records. Finally, a report summarizing the findings and variances would be generated.
Annual Inventory Count Key Findings
Item Category | Physical Count | Recorded Inventory | Variance | Explanation |
---|---|---|---|---|
Product A | 1000 | 980 | +20 | Discrepancy due to previous undercounting. |
Product B | 500 | 520 | -20 | Potential theft or damage. |
Product C | 200 | 205 | -5 | Minor counting error. |
Impact on Business Operations and Financial Statements
An accurate annual inventory count significantly impacts a company’s financial statements. Accurate inventory valuation directly affects the balance sheet, while the cost of goods sold calculation impacts the income statement and profitability. Accurate data ensures compliance with accounting standards.
Inventory count data informs crucial business decisions. Data on stock levels guides purchasing decisions, ensuring optimal inventory levels. Production planning is adjusted based on demand and available resources. Sales forecasting is refined based on historical sales data and current inventory levels.
The annual inventory count is crucial for complying with accounting standards like GAAP (Generally Accepted Accounting Principles) and IFRS (International Financial Reporting Standards). These standards dictate how inventory should be valued and reported on financial statements.
Accurate inventory data improves operational efficiency and cost management. Knowing precise stock levels minimizes storage costs, reduces waste from obsolescence, and prevents stockouts. This leads to optimized resource allocation and cost savings.
Inaccurate inventory counts negatively impact financial performance and decision-making. Overstated inventory inflates assets, potentially leading to an overvaluation of the company. Understated inventory underestimates costs and inflates profits, leading to inaccurate financial reporting and potentially legal repercussions.
Popular Questions
What are the legal implications of inaccurate inventory counts?
Inaccurate inventory counts can lead to misrepresentation of financial statements, potentially violating accounting regulations and leading to legal repercussions, including fines or penalties.
How often should a business conduct a full physical inventory count?
While an annual count is common, the frequency depends on factors like inventory turnover rate, industry regulations, and internal control requirements. Some businesses may opt for more frequent cycle counts.
What are some common causes of discrepancies during inventory reconciliation?
Common causes include data entry errors, theft, damage, obsolescence, and inaccurate initial inventory records.
How can technology improve the accuracy and efficiency of inventory counts?
Barcode scanners, RFID technology, and inventory management software significantly improve accuracy and efficiency by automating data collection and reducing manual errors.