Inventory Management Methods for Heavy Inventory Businesses
Accounting for inventory heavy businesses – Effective inventory management is crucial for businesses handling large volumes of stock. This section explores various inventory costing methods and systems for tracking inventory across multiple locations. Understanding these methods allows businesses to optimize profitability and comply with tax regulations.
Comparison of Inventory Costing Methods
Choosing the right inventory costing method significantly impacts a company’s reported profit and tax liability. Three common methods are First-In, First-Out (FIFO), Last-In, First-Out (LIFO), and Weighted-Average Cost.
Method | Calculation | Impact on Profit (High/Medium/Low Inventory Costs) | Tax Implications |
---|---|---|---|
FIFO (First-In, First-Out) | Assumes the oldest inventory is sold first. Cost of goods sold (COGS) reflects the cost of the oldest items. | Medium to High (depending on rising or falling prices) | Generally results in lower tax liability during periods of inflation, as COGS is lower. |
LIFO (Last-In, First-Out) | Assumes the newest inventory is sold first. COGS reflects the cost of the newest items. Note: LIFO is not permitted under IFRS. | Low to Medium (depending on rising or falling prices) | Generally results in higher tax liability during periods of inflation, as COGS is higher. |
Weighted-Average Cost | Calculates the average cost of all inventory items available for sale during a period. | Medium | Provides a relatively stable tax liability, regardless of price fluctuations. |
Inventory Tracking System using Bar Codes
A bar code system facilitates efficient inventory tracking across multiple warehouses. The process involves assigning unique bar codes to each item, integrating them into a database, and using barcode scanners at various stages.
- Receiving: Upon arrival, each item is scanned, its quantity is verified against the purchase order, and the data is updated in the inventory database.
- Storage: Items are stored in designated locations within the warehouse. The location is recorded in the database, linking it to the item’s bar code.
- Distribution: When an order is fulfilled, items are scanned, and the system updates inventory levels in real-time, reducing discrepancies and improving accuracy.
Just-in-Time (JIT) Inventory Management
JIT inventory management aims to minimize inventory holding costs by receiving materials only when needed for production. This approach is suitable for businesses with high inventory turnover.
- Advantages: Reduced storage costs, minimized obsolescence risk, improved cash flow.
- Disadvantages: Increased reliance on suppliers, potential production delays due to supply chain disruptions, higher risk of stockouts.
Cost Accounting for Inventory-Heavy Businesses
Accurate cost accounting is essential for determining profitability and making informed business decisions. This section details the calculation of cost of goods sold (COGS) and various cost allocation methods.
Calculating Cost of Goods Sold (COGS)
COGS represents the direct costs associated with producing goods sold during a period. For inventory-heavy businesses, this calculation often involves a high volume of transactions. The formula is generally: Beginning Inventory + Purchases – Ending Inventory = COGS. Direct costs include raw materials, direct labor, and manufacturing overhead directly attributable to the production process. Indirect costs, such as rent and utilities, are allocated using appropriate methods.
Cost Allocation Methods
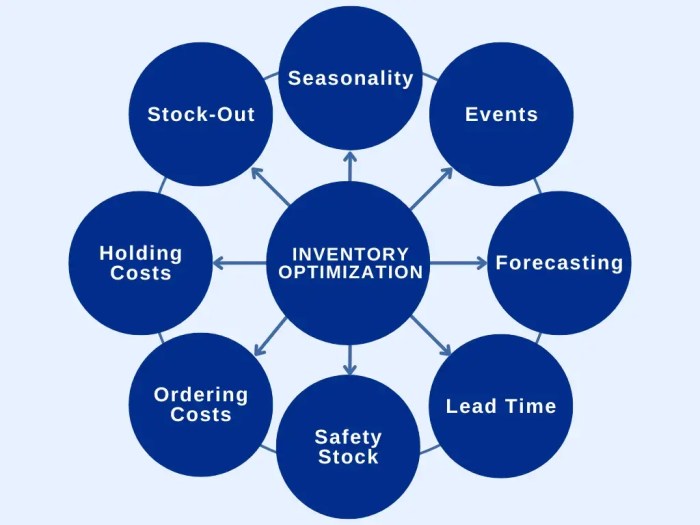
Source: cashflowinventory.com
Several methods exist for allocating indirect costs to products. The choice depends on the business’s specific circumstances and the level of detail required. Examples include:
- Activity-Based Costing (ABC): Allocates costs based on the activities involved in producing each product.
- Absorption Costing: Allocates both direct and indirect manufacturing costs to products.
- Variable Costing: Only allocates variable manufacturing costs to products.
Periodic Inventory Count
A periodic inventory count involves physically counting all inventory items at the end of a specific period. This is crucial for verifying inventory records and identifying discrepancies. A well-planned process includes:
- Preparation: Define the scope, assign teams, and gather necessary supplies.
- Counting: Conduct the count systematically, using barcode scanners or similar technology for efficiency.
- Verification: Compare the physical count with the inventory records and investigate any discrepancies.
- Documentation: Thoroughly document the entire process, including any adjustments made.
Inventory Valuation and Financial Reporting
Accurate inventory valuation is critical for reliable financial reporting. This section explores the impact of inventory write-downs and common accounting errors.
Impact of Inventory Write-Downs
Inventory write-downs occur when the market value of inventory falls below its carrying cost. This reduces the value of inventory on the balance sheet and impacts the income statement, reducing net income.
Scenario: A company valued its inventory at $100,000. Due to obsolescence, the market value dropped to $80,000. A $20,000 write-down is recorded, reducing inventory on the balance sheet and decreasing net income on the income statement.
Importance of Accurate Inventory Valuation, Accounting for inventory heavy businesses
Accurate inventory valuation ensures compliance with accounting standards (like GAAP or IFRS) and provides a reliable picture of the company’s financial health. Inaccurate valuations can lead to misstated financial statements, potentially impacting investor decisions and creditworthiness.
Common Inventory-Related Accounting Errors
Common errors include:
- Inaccurate counting: Leading to discrepancies between physical inventory and records.
- Incorrect cost allocation: Distorting the cost of goods sold and profitability.
- Failure to account for obsolescence: Overstating the value of inventory.
- Improper write-downs: Failing to adjust inventory value when market prices decline.
Technology and Inventory Management
Technology plays a significant role in enhancing inventory management efficiency. This section explores the use of ERP systems, inventory management software, and data analytics.
Enterprise Resource Planning (ERP) Systems
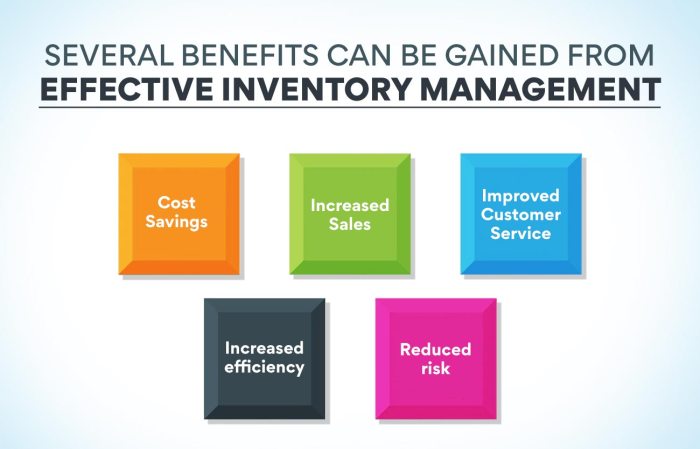
Source: edureka.co
Accurate inventory accounting is crucial for businesses heavily reliant on stock, impacting profitability and operational efficiency. Understanding inventory management principles is paramount, and a helpful resource for developing these skills might be the 7-eleven business leadership inventory test , which assesses leadership capabilities relevant to inventory control. Ultimately, mastering inventory accounting ensures a healthier bottom line for these types of enterprises.
ERP systems integrate various business functions, including inventory management, into a single platform. This improves data accuracy, streamlines processes, and provides a holistic view of inventory levels across different locations.
Inventory Management Software Features

Source: lerablog.org
Inventory management software offers various features to optimize inventory control.
Feature | Description | Benefits | Example Software |
---|---|---|---|
Demand Forecasting | Predicts future inventory needs based on historical data and trends. | Reduces stockouts and overstocking. | SAP, Oracle NetSuite |
Real-time Inventory Tracking | Provides up-to-the-minute visibility into inventory levels. | Improves decision-making and reduces delays. | Fishbowl Inventory, Zoho Inventory |
Automated Ordering | Automatically generates purchase orders when inventory levels fall below a predefined threshold. | Streamlines procurement and reduces manual effort. | Cin7, DEAR Inventory |
Data Analytics for Inventory Optimization
Data analytics can identify trends and patterns in inventory data, enabling businesses to optimize stock levels and reduce waste. Analyzing sales data, lead times, and demand forecasts allows for more accurate inventory planning.
Internal Controls and Inventory Security: Accounting For Inventory Heavy Businesses
Robust internal controls are crucial for protecting inventory assets from theft, damage, and obsolescence. This section Artikels a system of internal controls and security measures.
Internal Control System for Inventory
A comprehensive system includes:
- Segregation of duties: Different individuals should be responsible for purchasing, receiving, storing, and distributing inventory.
- Regular inventory counts: Periodic physical counts help detect discrepancies and potential theft.
- Access control: Restrict access to inventory storage areas to authorized personnel only.
- Inventory tracking system: Utilize a bar code or RFID system for accurate tracking.
- Regular audits: Conduct internal and external audits to ensure compliance with internal controls.
Physical Security Measures
Physical security measures, such as surveillance cameras, security alarms, and secure storage facilities, deter theft and damage.
Importance of Regular Inventory Audits and Reconciliation
Regular audits and reconciliation procedures ensure the accuracy of inventory records and help identify any discrepancies or weaknesses in the internal control system. This helps maintain inventory integrity and prevents financial losses.
FAQ Summary
What are the potential consequences of inaccurate inventory valuation?
Inaccurate inventory valuation can lead to misstated financial statements, impacting profitability, tax liabilities, and potentially attracting regulatory scrutiny. It can also hinder effective decision-making regarding purchasing, pricing, and production.
How often should a periodic inventory count be performed?
The frequency of periodic inventory counts depends on factors like inventory turnover rate, industry best practices, and internal control requirements. However, regular counts, at least annually, are generally recommended, with more frequent counts for high-value or high-risk items.
What are some common inventory-related accounting errors?
Common errors include inaccurate counting, improper cost allocation, failure to account for obsolescence or damage, and inconsistent application of inventory costing methods. Lack of proper documentation and inadequate internal controls also contribute to errors.
How can I choose the most appropriate cost allocation method?
The best cost allocation method depends on factors such as the nature of the inventory, the production process, and the company’s specific circumstances. Consult with an accounting professional to determine the most appropriate method for your business.