Inventory Management Methods for Small Businesses
Account for inventory of small business – Effective inventory management is crucial for the success of any small business. Understanding different inventory valuation methods and choosing the right inventory system are key steps in optimizing operations and profitability. This section will explore various methods, their advantages and disadvantages, and guide you through implementing both perpetual and periodic inventory systems.
Inventory Valuation Methods: FIFO, LIFO, and Weighted-Average Cost
Three primary methods are used to value inventory: First-In, First-Out (FIFO), Last-In, First-Out (LIFO), and Weighted-Average Cost. Each method impacts the cost of goods sold (COGS) and ultimately, the reported profit. The choice depends on factors like industry, tax implications, and the nature of the inventory itself.
Method | Advantages | Disadvantages | Example |
---|---|---|---|
FIFO (First-In, First-Out) | Simple to understand and implement; reflects current market prices for COGS; minimizes risk of obsolescence | Can inflate profits during periods of rising prices; may not accurately reflect the actual flow of goods | Imagine a bakery selling bread. FIFO assumes the oldest loaves are sold first. |
LIFO (Last-In, First-Out) | Reduces taxable income during inflation; matches current costs with current revenues | Can lead to lower net income; may not reflect the actual flow of goods; not permitted under IFRS | Using the bakery example, LIFO assumes the most recently baked loaves are sold first. |
Weighted-Average Cost | Simple to calculate; smooths out price fluctuations; less susceptible to manipulation | May not accurately reflect the cost of specific items; less accurate during periods of significant price changes | The bakery calculates the average cost of all loaves baked and uses that to determine the COGS. |
Implementing Perpetual vs. Periodic Inventory Systems
Small businesses typically choose between a perpetual or periodic inventory system. A perpetual system provides real-time inventory tracking, while a periodic system involves regular physical counts to determine inventory levels.
Perpetual Inventory System Implementation
- Set up an inventory tracking system: This could be a spreadsheet, dedicated software, or a combination.
- Record each item’s details: Include item name, SKU, cost, quantity.
- Update inventory levels continuously: Each time an item is received or sold, update the system.
- Regularly reconcile: Compare system data with physical counts to identify discrepancies.
Periodic Inventory System Implementation
- Schedule regular physical counts: Determine a frequency based on business needs (e.g., monthly, quarterly).
- Conduct a thorough count: Use standardized procedures to minimize errors.
- Compare physical count to records: Identify discrepancies and investigate causes.
- Adjust inventory records: Update records to reflect the physical count.
Simple Inventory Tracking Spreadsheet
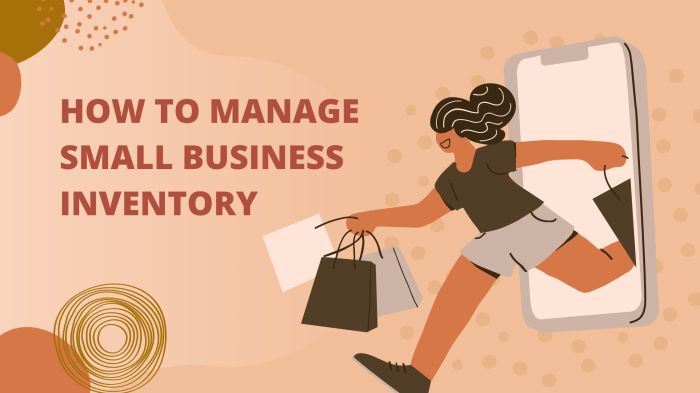
Source: amzaccountingsolutions.com
A basic spreadsheet can effectively track inventory. Columns should include item name, quantity on hand, cost per unit, and total value. Formulas can automatically calculate total value.
Item Name | Quantity on Hand | Cost per Unit | Total Value |
---|---|---|---|
Widget A | 100 | $5 | $500 |
Widget B | 50 | $10 | $500 |
Accurate Inventory Counting and Reconciliation: Account For Inventory Of Small Business
Regular and accurate inventory counts are vital for maintaining financial accuracy and preventing losses. This section will Artikel best practices for conducting these counts and reconciling them with recorded inventory levels.
Importance of Regular Physical Inventory Counts
Physical inventory counts help identify discrepancies between recorded and actual inventory levels. These discrepancies, often called shrinkage, can stem from theft, damage, errors in recording, or obsolescence. Regular counts allow for timely identification and correction of these issues, minimizing financial losses and improving operational efficiency.
Methods for Reconciling Physical Inventory Counts
Reconciliation involves comparing physical counts with recorded inventory levels. Common discrepancies include counting errors, data entry errors, and theft. Addressing discrepancies involves investigating the cause, adjusting records, and implementing preventative measures.
Physical Inventory Count Checklist
A structured checklist ensures consistency and accuracy during inventory counts. The checklist should include preparation steps, counting procedures, and post-count reconciliation.
- Preparation: Gather necessary materials (counting sheets, scanners, etc.), train personnel, and schedule the count during a slow period.
- Counting Procedures: Assign teams to specific areas, use two-person counting to minimize errors, and clearly label all counted items.
- Post-Count Reconciliation: Compare the physical count to the recorded inventory, investigate any discrepancies, and adjust inventory records.
Inventory Control and Optimization
Effective inventory control minimizes losses and ensures optimal stock levels. This section explores strategies to mitigate inventory shrinkage, utilize inventory management software, and calculate reorder points.
Causes and Mitigation of Inventory Shrinkage
Inventory shrinkage, the difference between recorded inventory and actual inventory, can result from theft, damage, obsolescence, and errors. Implementing robust security measures, improving storage practices, and regularly reviewing inventory levels are key mitigation strategies.
Benefits of Inventory Management Software
Inventory management software streamlines inventory processes, improving accuracy and efficiency. Features include real-time tracking, automated ordering, and reporting capabilities.
- Real-time tracking of inventory levels
- Automated reordering based on predefined parameters
- Detailed reporting and analysis of inventory data
- Integration with point-of-sale (POS) systems
Reorder Point Calculation, Account for inventory of small business
The reorder point is the inventory level at which a new order should be placed. It’s calculated considering lead time (time to receive an order), demand (rate of sales), and safety stock (buffer for unexpected demand).
Reorder Point = (Lead Time Demand) + Safety Stock
Example: If lead time is 2 weeks, weekly demand is 10 units, and safety stock is 5 units, the reorder point is (2 weeks
– 10 units/week) + 5 units = 25 units.
Impact of Inventory on Small Business Finances
Inventory significantly impacts a small business’s financial health. Accurate inventory accounting is crucial for determining COGS, profit margins, and cash flow. This section explores these relationships and strategies for managing inventory effectively.
Impact of Inaccurate Inventory Accounting on COGS and Profit Margins
Inaccurate inventory counts directly affect the calculation of COGS, which in turn impacts reported profit margins. Overstating inventory inflates profits, while understating it reduces profits. Accurate inventory accounting is crucial for accurate financial reporting.
Relationship Between Inventory Levels, Storage Costs, and Cash Flow
High inventory levels tie up capital, increasing storage costs and reducing cash flow. Conversely, low inventory levels can lead to stockouts and lost sales. Optimizing inventory levels balances the need to meet demand with minimizing storage costs and maximizing cash flow.
Managing Slow-Moving or Obsolete Inventory
Slow-moving or obsolete inventory represents a significant financial burden. Strategies for managing this include discounts, promotions, and potentially liquidating excess stock through online marketplaces or liquidators.
Technological Tools for Inventory Management
Technology plays a crucial role in modern inventory management. This section explores various software solutions, barcode scanning, RFID technology, and the integration of inventory management systems with POS systems.
Inventory Management Software Solutions
Numerous software solutions cater to the needs of small businesses. Key features to consider include ease of use, scalability, reporting capabilities, and integration with other business systems.
- User-friendly interface
- Real-time inventory tracking
- Automated ordering and alerts
- Reporting and analytics
- Integration with POS systems
Barcode Scanning and RFID Technology
Barcode scanning and RFID (Radio-Frequency Identification) technology significantly enhance inventory accuracy and efficiency. Barcode scanners provide quick and accurate data entry, while RFID tags allow for real-time tracking of items without manual scanning.
Integrating Inventory Management Software with POS Systems
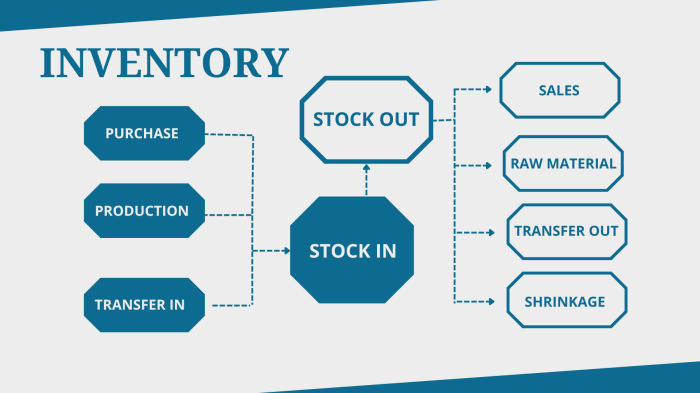
Source: cashflowinventory.com
Integrating inventory management software with a POS system provides real-time inventory updates, reducing discrepancies and improving efficiency. Sales data automatically updates inventory levels, eliminating manual data entry and potential errors.
Frequently Asked Questions
What is the difference between FIFO and LIFO?
Accurately accounting for inventory is crucial for any small business’s financial health. Understanding the impact of inventory management on profitability requires recognizing the four key roles inventory plays, as outlined in this helpful article: 4 important roles of inventory to a business. By grasping these roles, small businesses can refine their inventory accounting practices, leading to more accurate financial reporting and improved decision-making.
FIFO (First-In, First-Out) assumes the oldest inventory is sold first, while LIFO (Last-In, First-Out) assumes the newest inventory is sold first. This affects cost of goods sold and taxes.
How often should I conduct a physical inventory count?
The frequency depends on your business, but at least annually is recommended. More frequent counts (quarterly or monthly) are beneficial for businesses with high inventory turnover.
What is inventory shrinkage, and how can I prevent it?
Inventory shrinkage is the difference between the recorded inventory and the actual physical count, often due to theft, damage, or errors. Strong security measures, regular counts, and robust inventory tracking systems can help mitigate shrinkage.
Can I use spreadsheets for inventory management?
Spreadsheets can be useful for simple inventory tracking, but dedicated inventory management software offers more advanced features like automated ordering, reporting, and integration with other business systems.