Automating Inventory Control for Small Businesses
Automate inventory control for small business – Efficient inventory management is crucial for the success of any small business. Manual processes often lead to inaccuracies, lost sales, and increased costs. Automating inventory control offers a powerful solution, streamlining operations and boosting profitability. This article explores the benefits of automation, provides practical guidance on implementation, and showcases successful case studies.
Understanding Inventory Needs for Small Businesses, Automate inventory control for small business
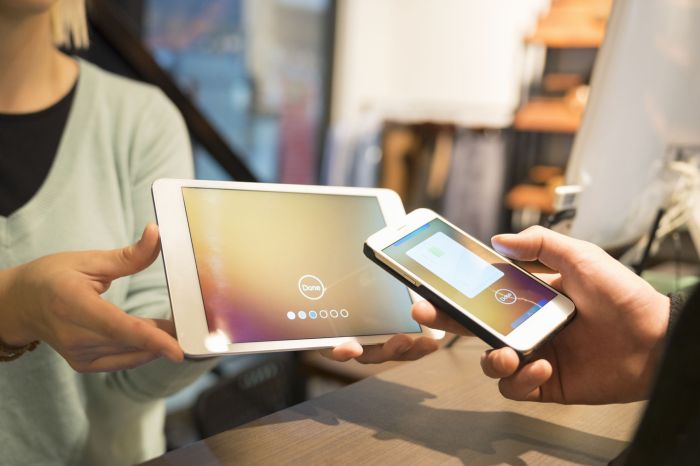
Source: entrepreneur.com
Small businesses frequently grapple with inventory challenges, including inaccurate stock counts, difficulty tracking sales, and inefficient ordering processes. These issues can significantly impact profitability and hinder growth. Three key metrics to monitor are inventory turnover rate, carrying costs, and stockout rate. Inaccurate inventory data directly impacts profitability by leading to overstocking (tying up capital and increasing storage costs), understocking (resulting in lost sales and dissatisfied customers), and inaccurate costing (affecting pricing strategies and profit margins).
Method | Cost | Time Savings | Accuracy |
---|---|---|---|
Manual Inventory Control | Low initial cost, but potentially high labor costs | Low | Low, prone to human error |
Automated Inventory Control | Higher initial investment in software and hardware, but lower long-term labor costs | High | High, minimizes human error |
Exploring Automation Solutions
Several software and tools automate inventory control, ranging from simple spreadsheet solutions to sophisticated enterprise resource planning (ERP) systems. Examples include Zoho Inventory, QuickBooks Online, and Xero. Cloud-based systems offer accessibility from anywhere with an internet connection, while on-premise systems require dedicated servers and IT infrastructure. An ideal system for a small retail business should include features like real-time tracking, barcode scanning, automated ordering, sales forecasting, and reporting capabilities.
A simple workflow diagram for automated inventory would show: 1. Receiving inventory (barcode scan upon arrival); 2. Stock updates in real-time (system automatically adjusts inventory levels); 3. Sales transactions (system updates inventory after each sale); 4. Low-stock alerts (system notifies users when stock reaches a predetermined level); 5.
Automated ordering (system generates purchase orders based on predefined parameters); 6. Reporting and analysis (system provides data on inventory turnover, sales trends, etc.).
Implementing Automation
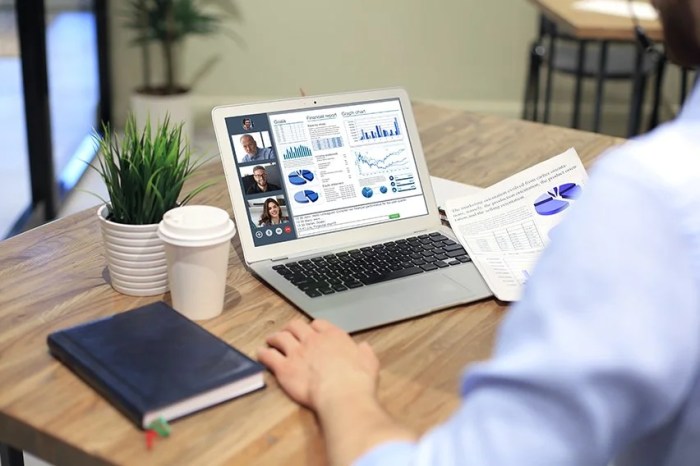
Source: freshbooks.com
Integrating an automated inventory system involves a phased approach. First, select appropriate software; then, thoroughly clean and migrate existing inventory data into the new system. This process requires careful attention to detail to avoid inaccuracies. Staff training is essential to ensure proficiency in using the new system. This training should cover all aspects of the software, from data entry to reporting.
A successful implementation checklist should include: software selection, data migration, staff training, testing, go-live, and ongoing support.
Cost-Benefit Analysis of Automation
Automating inventory control offers a significant return on investment (ROI). The initial investment in software and hardware is offset by reduced labor costs, minimized waste due to improved forecasting, and increased efficiency. This leads to higher profits and improved customer satisfaction due to faster order fulfillment and reduced stockouts. Automation offers both tangible benefits (e.g., reduced labor costs, increased efficiency) and intangible benefits (e.g., improved data accuracy, better decision-making).
- Reduced labor costs
- Minimized waste
- Improved accuracy
- Increased efficiency
- Better decision-making
- Enhanced customer satisfaction
Maintaining and Optimizing the System
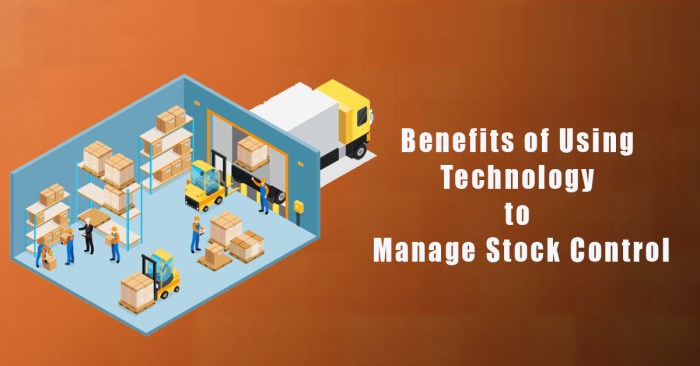
Source: revalsys.com
Ongoing system maintenance includes regular software updates, data backups, and security measures to protect sensitive data. Monitoring system performance involves tracking key metrics and identifying areas for improvement. Regular data audits ensure accuracy and integrity. Best practices include implementing robust data validation rules and establishing clear procedures for handling discrepancies.
Case Studies of Successful Implementations
Consider a small bookstore that previously relied on manual inventory tracking. Before automation, stockouts were frequent, leading to lost sales and customer frustration. Inventory counts were inaccurate, resulting in overstocking of slow-moving titles and understocking of popular ones. After implementing an automated system with barcode scanning and real-time updates, stockouts decreased by 75%, while inventory accuracy increased to 98%.
Order fulfillment time reduced by 50%, leading to improved customer satisfaction.
- 75% reduction in stockouts
- 98% increase in inventory accuracy
- 50% reduction in order fulfillment time
- Significant increase in customer satisfaction
- Improved sales and profitability
FAQ Overview: Automate Inventory Control For Small Business
What are the common signs that my small business needs automated inventory control?
Automating inventory control offers significant benefits to small businesses, streamlining operations and reducing costs. Understanding the tax implications is crucial, however, so it’s important to know whether or not are businesses inventory taxed in your specific region. This knowledge allows for accurate financial planning and ensures compliance, further enhancing the effectiveness of your automated inventory system.
Recurring stockouts, frequent inventory discrepancies, excessive manual data entry, difficulty forecasting demand, and slow order fulfillment are all indicators.
How much does inventory management software typically cost?
Costs vary greatly depending on features, scalability, and vendor. Expect a range from free options with limited functionality to several hundred dollars per month for comprehensive solutions. Many offer free trials.
What if my employees are resistant to using new software?
Thorough training, clear communication of benefits, and ongoing support are key. Addressing concerns and providing ample opportunity for practice will foster adoption.
Can I integrate my inventory system with my existing point-of-sale (POS) system?
Many inventory management systems offer seamless integration with popular POS systems, improving data accuracy and streamlining operations. Check for compatibility before purchasing.