Perpetual Inventory Systems: A Comprehensive Guide
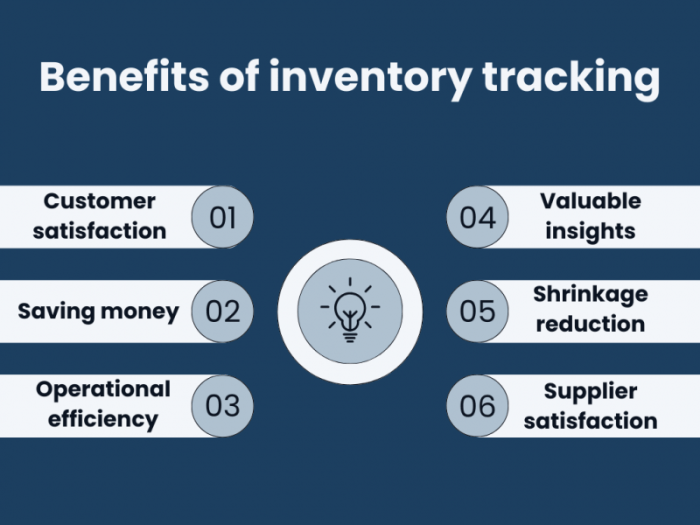
Source: synder.com
Assuming the business maintains a perpetual inventory system, accurate stock levels are readily available. This is crucial for efficient operations, especially considering external factors; for instance, the question of whether are home inspections busy when there is low housing inventory could impact the demand for certain inspection-related supplies. Therefore, a robust perpetual inventory system allows for proactive adjustments to inventory based on market fluctuations.
This article provides a detailed overview of perpetual inventory systems, encompassing their core principles, advantages, costing methods, management techniques, impact on financial reporting, and crucial internal controls. Understanding perpetual inventory systems is essential for businesses seeking accurate and real-time inventory tracking, leading to improved financial decision-making.
Understanding Perpetual Inventory Systems
A perpetual inventory system continuously tracks inventory levels throughout the year. Unlike periodic systems, which only update inventory at the end of a period, perpetual systems provide real-time visibility into stock quantities, costs, and sales data. This real-time tracking allows for more effective inventory management and improved forecasting.
The primary advantage of a perpetual system lies in its ability to provide up-to-the-minute inventory data. This enables businesses to make informed decisions about purchasing, production, and pricing. In contrast, periodic systems rely on physical counts at the end of the period, creating a lag in information and potentially leading to stockouts or overstocking.
Key differences between perpetual and periodic systems include record-keeping and cost accounting. Perpetual systems require continuous updates to inventory records with each transaction (purchase, sale, return), while periodic systems only update records at the end of a period. This difference impacts cost of goods sold (COGS) calculation; perpetual systems calculate COGS continuously, whereas periodic systems calculate it based on the beginning and ending inventory values.
Businesses that benefit most from perpetual inventory systems are those with high inventory turnover, high-value items, or a need for precise inventory control. Examples include retail stores with numerous SKUs, manufacturing companies tracking raw materials and finished goods, and businesses operating in industries with high theft or spoilage risk.
Business Type | Inventory Type | Reasons for Perpetual System | Potential Challenges |
---|---|---|---|
Retail Store (Electronics) | High-value consumer electronics | Real-time sales tracking, accurate inventory levels for optimal pricing and preventing stockouts, reduced shrinkage through tighter control. | High implementation cost, requires robust technology infrastructure, potential for data entry errors. |
Pharmaceutical Wholesaler | Prescription drugs | Strict regulatory compliance requiring precise inventory tracking, prevention of expired or damaged goods, efficient lot tracking. | Complex inventory management due to expiration dates, high accuracy requirements, stringent audit trails. |
Auto Parts Supplier | Fast-moving auto parts | Quick identification of popular items, timely replenishment, optimized warehouse space utilization. | High volume of transactions, potential for stock discrepancies due to fast-paced operations, maintaining accurate pricing data. |
Jewelry Store | High-value jewelry | Enhanced security, precise tracking of valuable items, minimizes loss due to theft or damage. | High cost of implementing security features, strict internal control measures required, insurance considerations. |
Costing Methods under Perpetual Inventory
Several costing methods are applicable under a perpetual inventory system, each impacting the cost of goods sold (COGS) and ending inventory valuation. The most common methods are First-In, First-Out (FIFO), Last-In, First-Out (LIFO), and Weighted-Average Cost.
FIFO assumes that the oldest inventory items are sold first, while LIFO assumes the newest items are sold first. The weighted-average cost method calculates the average cost of all inventory items available for sale and applies this average cost to both COGS and ending inventory. The choice of method significantly affects the reported COGS and net income, influencing tax liabilities and financial statement analysis.
Consider a scenario where a company purchases and sells units of a product:
- Beginning Inventory: 10 units @ $10 each
- Purchase 1: 20 units @ $12 each
- Purchase 2: 15 units @ $15 each
- Sale 1: 25 units
- Sale 2: 10 units
FIFO Calculation:
- COGS for Sale 1: (10 units x $10) + (15 units x $12) = $280
- COGS for Sale 2: (10 units x $12) = $120
- Ending Inventory: (5 units x $15) = $75
LIFO Calculation:
- COGS for Sale 1: (15 units x $15) + (10 units x $12) = $330
- COGS for Sale 2: (10 units x $12) = $120
- Ending Inventory: (10 units x $10) = $100
Weighted-Average Calculation:
- Total Units: 45 units
- Total Cost: (10 x $10) + (20 x $12) + (15 x $15) = $550
- Weighted-Average Cost: $550 / 45 units = $12.22 (approximately)
- COGS for Sale 1: 25 units x $12.22 = $305.50
- COGS for Sale 2: 10 units x $12.22 = $122.20
- Ending Inventory: 10 units x $12.22 = $122.20
The choice of costing method impacts the reported COGS and net income, influencing financial ratios and tax obligations. For example, during periods of inflation, FIFO will generally result in a lower COGS and higher net income compared to LIFO.
Inventory Management Techniques
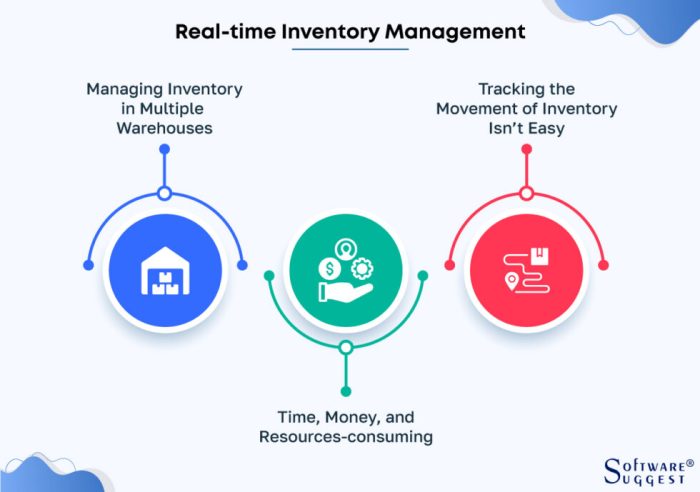
Source: softwaresuggest.com
Effective inventory management is crucial for businesses using a perpetual inventory system. This involves implementing techniques to optimize stock levels, minimize waste, and ensure accurate record-keeping. Technology plays a significant role in enhancing efficiency and accuracy.
Common inventory management techniques include ABC analysis (prioritizing inventory based on value), Economic Order Quantity (EOQ) calculations (determining optimal order sizes), and Just-in-Time (JIT) inventory management (minimizing inventory holding costs). Barcode scanners and RFID technology enable real-time tracking of inventory movement, improving accuracy and reducing manual data entry errors.
Potential inventory discrepancies, such as theft, damage, or errors in recording transactions, can be identified through regular cycle counting, reconciliation of physical inventory with system records, and variance analysis. Discrepancies should be investigated and resolved promptly to maintain the accuracy of inventory records.
A hypothetical inventory management plan for a small retail store using a perpetual system might include:
- Daily stock updates using barcode scanners.
- Weekly cycle counts of high-value items.
- Monthly reconciliation of physical inventory with system records.
- Automated stock replenishment system triggered by low stock alerts.
- Regular review of sales data to adjust ordering patterns.
- Security measures to prevent theft and damage.
Impact on Financial Reporting, Assuming the business maintains a perpetual inventory system
A perpetual inventory system directly impacts the preparation of financial statements. The continuous tracking of inventory allows for more accurate reporting of COGS on the income statement and ending inventory on the balance sheet. Accurate inventory valuation is essential for determining profitability and assessing the financial health of the business.
Inventory valuation affects profitability by influencing the COGS calculation. A higher COGS reduces net income, while a lower COGS increases net income. The choice of costing method (FIFO, LIFO, weighted-average) significantly impacts inventory valuation and consequently the reported profitability.
Accounting entries for inventory transactions under a perpetual system include:
- Purchase: Debit Inventory, Credit Accounts Payable (or Cash).
- Sale: Debit Accounts Receivable (or Cash), Credit Sales Revenue; Debit COGS, Credit Inventory.
- Return: Debit Accounts Payable (or Cash), Credit Inventory; Debit Sales Returns and Allowances, Credit Accounts Receivable (or Cash).
The timing of inventory cost recognition differs between perpetual and periodic systems. Perpetual systems recognize COGS at the time of each sale, while periodic systems recognize COGS at the end of the accounting period based on the beginning and ending inventory values. This difference can affect the timing of reported income and expenses.
Internal Controls and Audits
Strong internal controls are essential for maintaining the accuracy of perpetual inventory records and preventing errors or fraud. These controls help to ensure that inventory data is reliable and that the financial statements accurately reflect the company’s financial position.
Examples of internal controls include segregation of duties (separating inventory control from accounting functions), regular physical inventory counts, use of barcodes or RFID tags for tracking inventory, and access controls to restrict unauthorized access to inventory. These controls help prevent inventory shrinkage, theft, and data manipulation.
Auditors use various procedures to verify the accuracy of perpetual inventory records, including observing inventory counts, testing the accuracy of inventory records, and reviewing internal controls. They may perform test counts, examine supporting documentation, and analyze inventory turnover ratios to assess the reliability of the inventory data.
Weak internal controls can have a significant impact on financial reporting under a perpetual inventory system. This can lead to inaccurate inventory valuations, misstated COGS, and ultimately, unreliable financial statements. This can negatively impact investor confidence, credit ratings, and regulatory compliance.
Key Questions Answered: Assuming The Business Maintains A Perpetual Inventory System
What are the potential downsides of a perpetual inventory system?
Implementation costs can be high, requiring investment in software and training. Maintaining accuracy demands meticulous record-keeping and robust internal controls; errors can be costly to rectify.
How frequently should cycle counts be performed in a perpetual system?
Frequency depends on the business and inventory type. High-value or fast-moving items may require more frequent counts (e.g., weekly or monthly), while slower-moving items might be counted less often (e.g., quarterly).
Can a small business effectively use a perpetual inventory system?
Yes, many affordable software solutions exist that cater to small businesses. The key is selecting a system that aligns with the business’s needs and resources.
How does a perpetual inventory system impact tax reporting?
It provides more accurate data for calculating cost of goods sold, leading to a more precise determination of taxable income.