The Importance of Inventory Control Systems for Businesses: 1. One Reason Businesses Need An Inventory Control System Is
1. one reason businesses need an inventory control system is – One reason businesses need an inventory control system is to streamline operations and enhance profitability. Effective inventory management is crucial for minimizing costs, improving efficiency, boosting customer satisfaction, facilitating better decision-making, and ultimately, strengthening financial performance. This article delves into these key benefits in detail.
Reduced Costs and Waste, 1. one reason businesses need an inventory control system is
Implementing a robust inventory control system significantly reduces costs and minimizes waste through optimized stock management. By accurately tracking inventory levels, businesses can prevent both stockouts and overstocking, two common sources of financial drain.
Stockouts lead to lost sales opportunities and dissatisfied customers. For example, a retail store running out of a popular product during peak season misses potential revenue and risks losing customers to competitors. Conversely, overstocking ties up valuable capital in unsold goods, increasing storage costs, and potentially leading to spoilage or obsolescence, especially for perishable items or products with short shelf lives.
Consider a grocery store holding excess perishable produce; unsold items will spoil, resulting in direct financial losses and waste disposal costs.
Optimizing inventory levels involves employing strategies like forecasting demand, implementing just-in-time inventory management, and using data analytics to identify slow-moving items. This allows businesses to maintain sufficient stock to meet customer demand without excessive surplus. Regularly reviewing inventory and adjusting stock levels based on sales data is also critical in reducing waste.
Cost Category | Understocking | Overstocking |
---|---|---|
Lost Sales Revenue | High | Low |
Storage Costs | Low | High |
Spoilage/Obsolescence Costs | Low | High |
Customer Dissatisfaction | High | Low |
Improved Operational Efficiency
Real-time inventory tracking and data analysis are pivotal in improving operational efficiency. Efficient inventory management translates to faster order fulfillment, streamlined warehouse processes, and enhanced employee productivity.
- Real-time inventory tracking enables faster order fulfillment: Knowing the exact location and quantity of items allows for quick order processing and reduces picking and packing time.
- Inventory data streamlines warehouse operations: Data analysis helps optimize warehouse layout, improve storage strategies, and reduce unnecessary movement of goods.
- Efficient inventory management improves employee productivity: Clear inventory systems reduce time spent searching for items, resolving discrepancies, and managing stock levels, freeing up employees to focus on other tasks.
Implementing an inventory control system in a small business involves a phased approach:
- Choose an appropriate inventory management software or system.
- Conduct a thorough inventory count and data entry.
- Set up a system for tracking inventory movements (incoming and outgoing).
- Establish reorder points and lead times for each item.
- Regularly review and adjust inventory levels based on sales data and forecasts.
Enhanced Customer Satisfaction
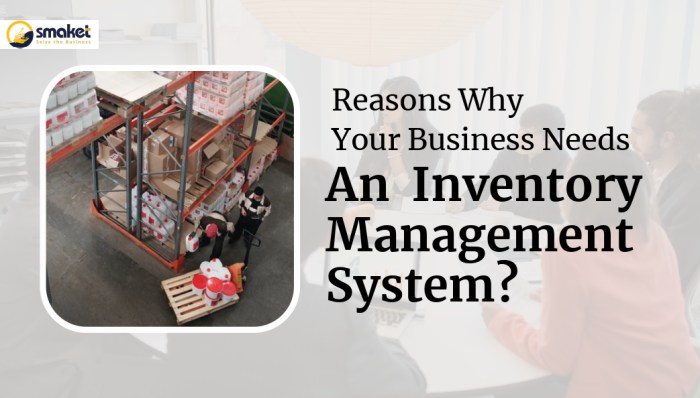
Source: smaket.org
Accurate inventory data directly impacts customer satisfaction. Reliable inventory information ensures order accuracy, on-time delivery, and readily available products, leading to improved customer service and loyalty.
Accurate inventory data leads to better order accuracy and on-time delivery, which are crucial for customer satisfaction. Conversely, poor inventory management results in stockouts, backorders, and inaccurate order fulfillment, leading to frustrated customers, negative reviews, and lost business. For instance, a customer expecting a product for a timely event will be highly dissatisfied if the order is delayed due to inventory inaccuracies.
Metric | Before Inventory Control System | After Inventory Control System |
---|---|---|
On-time Delivery Rate | 70% | 95% |
Order Accuracy Rate | 85% | 98% |
Customer Satisfaction Score (CSAT) | 3.5/5 | 4.5/5 |
Better Decision Making
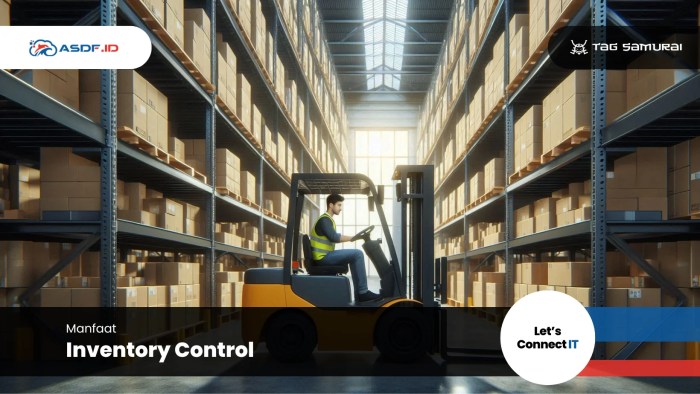
Source: asdf.id
Inventory data provides crucial insights for informed purchasing decisions, preventing both stockouts and excess inventory. Analysis of inventory data also helps identify slow-moving or obsolete items, enabling businesses to adjust their strategies accordingly.
Inventory analysis helps identify slow-moving or obsolete items, allowing businesses to implement strategies such as discounts or clearance sales to reduce excess inventory. This data also informs purchasing decisions, preventing future stockouts or overstocking. For example, analyzing sales trends can help predict future demand, enabling businesses to order appropriate quantities of products.
A visual representation of the impact of accurate inventory data on sales forecasting would show a graph comparing actual sales versus forecasted sales. With accurate inventory data, the forecasted sales line would closely align with the actual sales line, indicating improved prediction accuracy and reduced forecasting errors.
Stronger Financial Performance
Improved inventory management significantly contributes to a healthier cash flow and stronger financial performance. Accurate inventory valuation is crucial for reliable financial reporting.
Improved inventory management directly impacts cash flow by reducing the capital tied up in excess inventory. Accurate inventory valuation is crucial for generating accurate financial statements, ensuring compliance with accounting standards, and facilitating informed financial decision-making. A comparison of financial statements of a business with and without a robust inventory control system would show a significant improvement in key metrics like inventory turnover, gross profit margin, and return on assets in the business with effective inventory management.
Financial Metric | Without Inventory Control | With Inventory Control |
---|---|---|
Inventory Turnover | 2.0 | 4.5 |
Gross Profit Margin | 25% | 35% |
Return on Assets (ROA) | 10% | 18% |
Integrating inventory control data into the business’s overall financial planning process involves:
- Regularly reviewing inventory levels and costs in relation to sales.
- Using inventory data to forecast future cash flow and budgeting.
- Incorporating inventory valuation methods into financial reporting.
- Analyzing inventory turnover ratios and other key performance indicators (KPIs) to identify areas for improvement.
Query Resolution
What are some common signs that a business needs an inventory control system?
Frequent stockouts, excessive storage costs, high levels of waste due to spoilage or obsolescence, inaccurate sales forecasts, and difficulty meeting customer demand are all indicators.
How much does an inventory control system typically cost?
Costs vary greatly depending on the size of the business, the complexity of the system, and whether it’s a cloud-based or on-premise solution. Expect a range from free basic solutions to several thousand dollars for more comprehensive systems.
Can small businesses benefit from inventory control systems?
Absolutely. Even small businesses can benefit significantly from improved efficiency, reduced waste, and better decision-making, regardless of scale.
How long does it take to implement an inventory control system?
Implementation time varies depending on the system’s complexity and the business’s size. Simple systems might be implemented within weeks, while more complex ones could take months.